Inside Dyson — I just got an inside look of the company that reinvented the vacuum
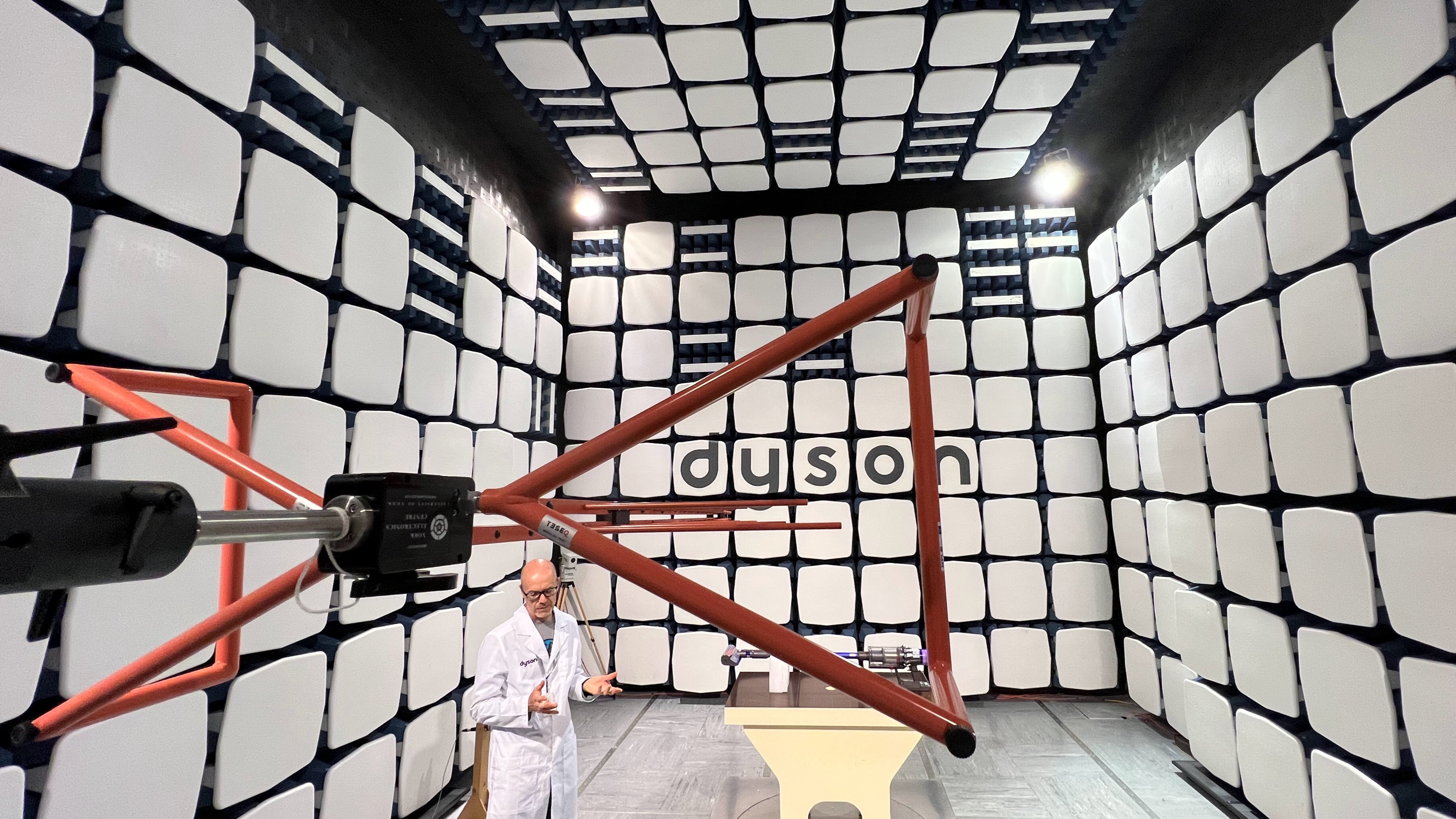
Much like Apple devices, Dyson products tend to be a little pricier compared to those of its rivals. And you may think that’s because Dyson is trading on its brand power much like Apple.
There may be some truth in that. But I recently got a rare tour of Dyson’s U.K. headquarters, just outside of the picturesque market town of Malmesbury in England’s Wiltshire — hardly an area known for cutting-edge technology or engineering. Having got a first-hand look at the near-obsessive approach Dyson takes to engineering its products, specifically vacuum cleaners, it’s now easy to see why the company charges premium prices.
Let me take you on a journey of what I saw and found poking through Dyson's pseudo campus on a damp English afternoon.
Dyson: They breed their own dust mites
A big part of Dyson’s work is focussed around looking really hard at dust, especially at dust mites, which are allergen-making machines due to their allergy-triggering droppings.
Filled with particulate counters and measuring equipment. testing is carried down to 20 nanometers, which is far beyond testing standards.
Dyson does this in a microbiology lab that looks a little like the lab from the start of 28 Days Later, only rather than deal with sci-fi viruses, the technicians handle a variety of dust and dust mites.
Peering into a microscope I got a glimpse at dust mites first hand, going about their business; they struck me as both industrial and rather creepy, as these critters could be crawling all over your home if you’re not handy with a vacuum. (Check out our handy guide on how to clean every room of your home.)
Dust mites are bred and grown in the labs with Dyson using them to test how well its filtration devices work and what gets sucked up.
Get instant access to breaking news, the hottest reviews, great deals and helpful tips.
Dyson employees can even bring in their own dust for testing, something which bemused me a little — you don't want to be the person with the most mites… or maybe you do as you can go to town with a Dyson V15.
The £3 million separation systems lab furthers this work. This is where Dyson vacuum filtration is tested in order to achieve 99% filtration.
But at the same time the technicians also target the avoidance of any loss in suction, something Dyson has long prided itself in doing.
Filled with particulate counters and measuring equipment. testing is carried down to 20 nanometers, which is apparently far beyond testing standards. And as a result, there are multiple layers of filtration taking place even in compact Dyson vacuums.
I got to see a cross-section of a hand-held Dyson stick vacuum, and it really showed off just how complex the engineering is; this isn’t any simple suck then dump into a container system.
Such filtration is needed as Dyson wants to ensure that expelled air from its vacuums is pretty much as pure as it can be, and make sure while dust is grabbed that bacteria isn’t expelled either.
Getting just the right sound
Of course, testing isn't limited to dust and filtration, Dyson also works to make sure its devices don’t interfere with other electronics, while also tuning its vacuums to sound just right.
Dyson said it could make a pretty much soundless vacuum, but that was seen as unsettling for users who want to hear something to know their vacuum is doing the job.
To do the former, Dyson has a rather slick looking electromagnetic compatibility (EMC) testing room. What’s effectively a metal box to keep out external electromagnetic interference, Dyson can then test the electromagnetic emissions of its devices, right down to the compact digital motors it uses in the likes of the Dyson V10.
An antenna measures the electromagnetic emissions and then feeds it back to the computer in a separate room. This allows the engineers to test to a variety of EMC standards, which can vary from nation to nation. It can also get a sense of the EMC given off — stick vacuums cause radiated EMC while hair care products cause conductive emissions.
Doing this means Dyson products being developed by the R&D department can be prototyped and tested for EMC standards to ensure they are practical to bring to the market.
And why is EMC important? Well in a world where we are surrounded by electronic devices, ensuring they don’t all interfere with each other is crucial; older readers will remember how incoming calls and text messages used to mess with audio equipment.
On the sound side, a semi-anechoic chamber (a room built to stop echoes) is used to calibrate the noise and sound quality of Dyson devices.
With walls coated in angular sound absorbing materials, a Dyson device is placed in the middle and surrounded by an array of 10 microphones known as an audio hemisphere.
From this setup sound engineers can hear exactly what, say a Dyson vacuum, sounds like. And with that they can calibrate the audio output accordingly.
Interestingly, Dyson said it could make a pretty much soundless vacuum, but that was seen as unsettling for users who want to hear something to know their vacuum is doing the job. Also different people prefer different sound profiles; British and Europeans tend to prefer less noisy vacuums, while Americans have a preference for louder machines as it gives the impression of serious power.
Welcome to Dyson's prototype paradise
Of course, before all this testing there’s the prototyping stage.
While I didn't get to see product designers at work, I did get to see the areas where new parts are made for prototype devices, using a mixture of industrial machines for working with metals to 3D printing with lasers.
Using this approach means Dyson can create prototype parts and devices without the need to create the tooling for full manufacturing, though there is a machine shop available if that needs to be done.
This gives Dyson that classic fail fast approach that some start-ups love to embrace by making mistakes at prototype level aren’t expensive problems. But plenty of 3D simulation is still used before any physical prototyping takes place as well.
A mix of engineers said how they come up with ideas for fine tuning parts or developing new brush heads or products, and the ability to rapidly prototype those means they can quickly see if their ideas are worth pursuing.
And will all this equipment at their disposal, engineers can quickly create test parts with very fine elements, all within the Malmesbury facility.
Solid bits of metal can be turned into fine parts, ready to test without the need for more costly processes like injection moulding.
Seeing this in action is rather fascinating, and really communicates how complex Dyson's products are; these are not simply things relying on a big brand name to do the heavy lifting.
Rolling out the (testing) carpet
The coolest thing about the lab is the use of a high-speed camera that can capture slow-motion footage of what's going on at the suction and brush area of the vacuums being tested.
Probably my favorite part of the tour was the £1 million pickup lab. This environmentally controlled area comprises a suite of testing lanes used to see just how well a Dyson vacuum picks up a variety of dust, debris and more.
Such testing is needed to meet industry standards, whereby debris must be collected in five passes of a vacuum. But Dyson aims to do this in one.
The cool thing about the lab is the use of a high-speed camera that can capture slow-motion footage of what's going on at the suction and brush area of the vacuums being tested. This gives Dyson’s engineers (quite literally) a granular look at how dust is being sucked up, thereby allowing for more fine tuning.
Such tuning is needed, as taking a look at a cupboard full of debris and dust the engineers use for testing, there's a lot a Dyson vacuum needs to suck up and suck up well.
For example, the lab holds two different variations of Cheerios cereal. The reason for that is, Cheerios in the U.S. are bigger than they are in the U.K. so it presents a different challenge for Dyson vacuums.
By testing this, Dyson can ensure its vacuums do the job asked of them, regardless of where they are on the globe; well, the markets Dyson operates in at least.
This attention to detail and the level of testing and prototyping really helps convey the idea that Dyson is taking its products very seriously, maybe to the level of obsession.
Dyson diploma
This level of dedication to craft isn't all that surprising when you realize that Dyson’s U.K. HQ also includes the Dyson Institute of Engineering and Technology.
Established in 2017, this form of corporate university saw its first cohort of graduates last year. While only numbering 33, all these grads had jobs guaranteed at Dyson, and all accepted them.
Now Malmesbury isn’t the most exciting of towns for youthful university-level exuberance (trust me, my parents live there), though it’s a short hop to the university cities of Bath and Bristol. But for budding engineers, the course and Institution has its perks.
For a start, there are no university fees, which have ballooned in the U.K. since I graduated in 2010. And to sweeten the deal further, students are paid a salary and also have a job guaranteed for them at Dyson. The cherry on top is some rather neat-looking student accommodation, with ensuite rooms and comfortable living quarters, as well as a whole lot of Dyson kit.
To some that might seem like Dyson is monopolizing some of the U.K. upcoming engineers of the future. And for those lucky enough to earn one of the limited spots, they may feel there's some metaphorical Kool-Aid drinking required. But Apple does the same in the States, with Apple University. So it’s not hard to see the so-called Apple of Appliances would do the same.
Pottering around the ‘campus,’ it’s easy to see why Dyson might be compared to Apple. Its employees are all enthused about the brand and the work they do, even when I quietly listened into some conversations.
There's a wealth of freshly prepared food at the canteens (something that reminded me of my visit to Google HQ in Mountain View, California), in addition to an on-site salon and doctor to make life easier for Dyson workers; with all these perks coming to work seems almost a treat.
While Dyson has a level of secrecy that’s akin to Apple, it also has its own flavor.
This ranges from the BAC Lightning F.1A. hanging in one of the cafeterias and the Harrier fighter jet sitting in one of the car parks — both nodding towards sky-high points in British engineering — to the openness some of the workers exude when talking about their approach to work and the challenges they aim to tackle.
And this is why it's exciting to see Dyson’s latest products, even the very odd but well-engineered Dyson Zone, as I’ve got a glimpse at the minds and processes that power the innovation behind the devices we can sometimes take for granted.
So while I bemoan how Apple may have me worried about the iPhone 14 and the lack of progress, its nearest U.K. equivalent still seems to be a trailblazer, even some 33 years after first starting out.
Next: Dyson Zone is official: find out the price and release date. Also check out this Dyson vacuum cleaner that is a sci-fi tech marvel — and I love it.
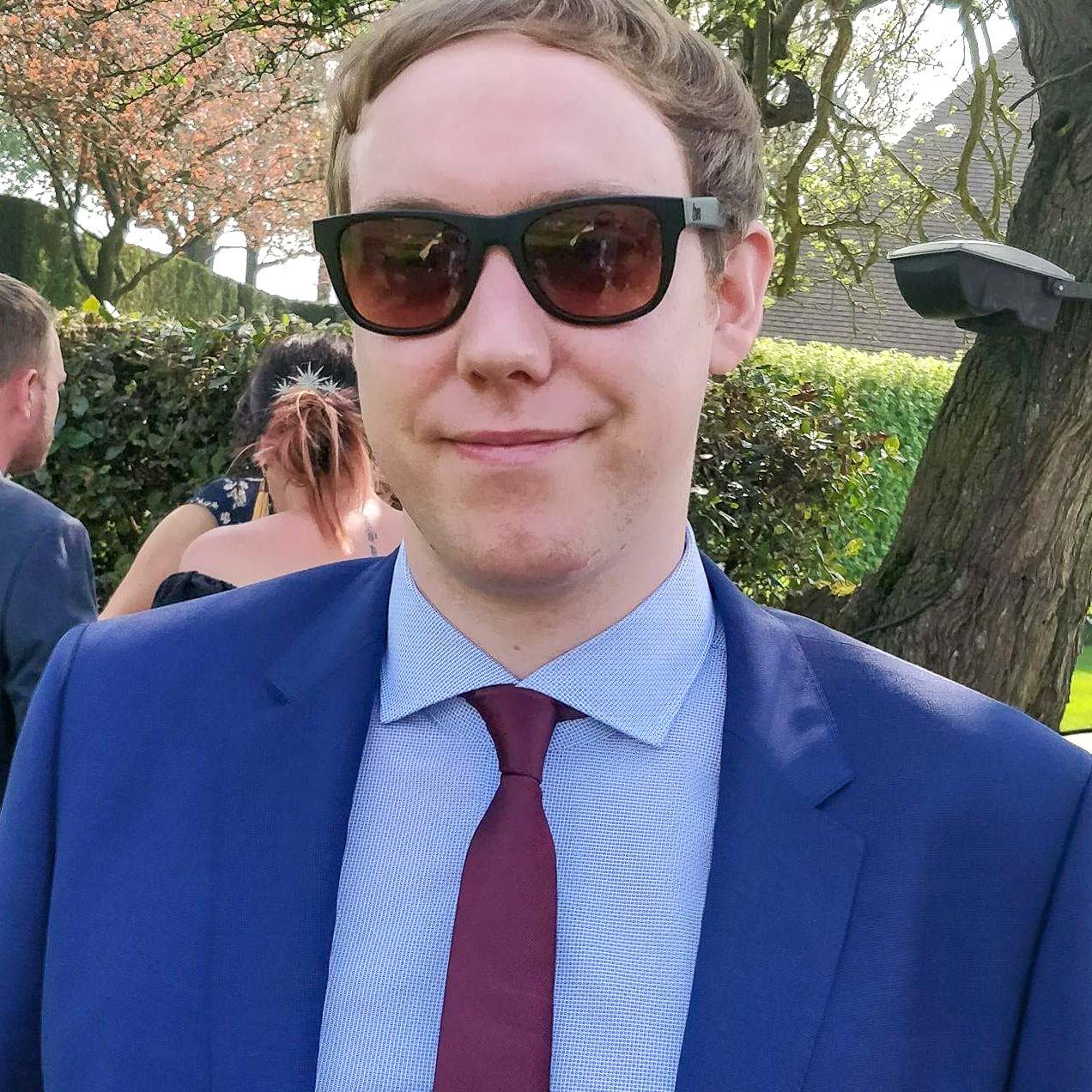
Roland Moore-Colyer a Managing Editor at Tom’s Guide with a focus on news, features and opinion articles. He often writes about gaming, phones, laptops and other bits of hardware; he’s also got an interest in cars. When not at his desk Roland can be found wandering around London, often with a look of curiosity on his face.