Special Report
Latest Special Report
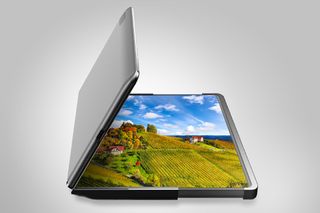
Samsung CES 2023 press conference: Everything that was announced
By Nick Pino last updated
Curious to see what Samsung's up to at CES 2023? We're watching the keynote live and have all the details.
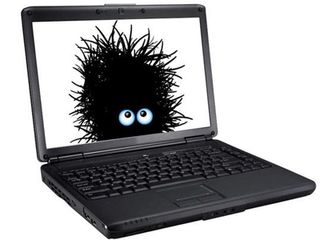
Do you really need to pay for antivirus software?
By John R. Quain published
You can get plenty of good antivirus software for free, but paid antivirus products, with their more elaborate system behavior monitors, are more likely to pick up on new threats.
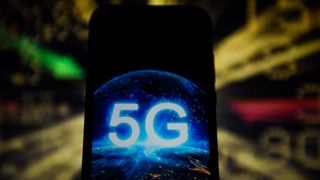
When is 5G coming to you? The definitive guide to the 5G network rollout
By Tom's Guide Staff published
Carriers are building out their 5G coverage, but when is faster 5G coming to you? Here's everything you need to know about what 5G is and what to expect from it.
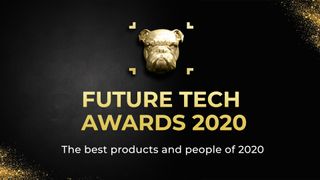
The Future Tech Awards have arrived with support from five special sponsors
By Sponsored published
The Future Tech Awards have landed at CES 2021. Read more about the standouts of CES 2021.
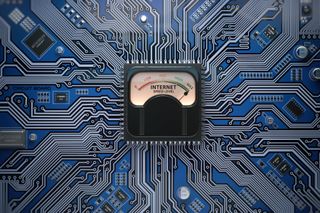
What Is Gig-Speed Internet?
By Brian Westover published
Get up to speed on the best thing to happen to high-speed internet service.
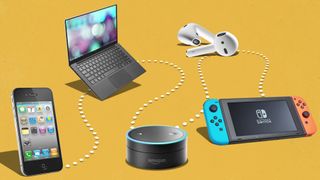
The 15 best tech products of the decade
By Tom's Guide Staff published
Here are the best tech products of the decade, including the Amazon Echo Dot, Apple AirPods and Nintendo Switch.
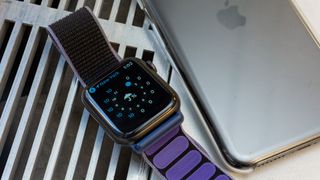
My first month with an Apple Watch: Series 5 made me a believer
By Henry T. Casey published
Here's how my first month with a wearable device went, what I loved and what I want Apple to change in the Apple Watch 6.
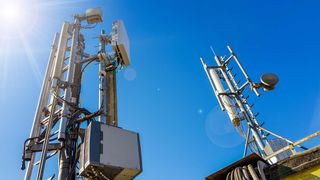
5G Dangers: What the Experts Say About Health Risks
By Caitlin McGarry published
Is there cause for concern?
Sign up to get the BEST of Tom’s Guide direct to your inbox.
Upgrade your life with a daily dose of the biggest tech news, lifestyle hacks and our curated analysis. Be the first to know about cutting-edge gadgets and the hottest deals.